Permanent magnet rotor e1655961736623.jpeg.
Drive motors are the mainstay in our day-to-day life. In drive motors, the Permanent Magnet Brushless DC (PMBLDC) motors are more prominent. It has excellent torque-speed characteristics. Compared to others, it has less maintenance cost. The Cogging torque is one of the crucial obstructions in PMBLDC Motor. It has always been a …
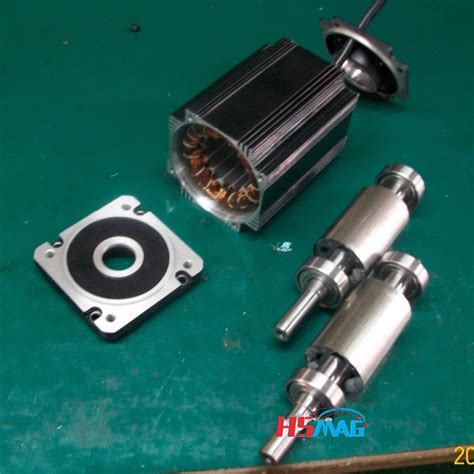
2.2 External rotor permanent magnet motor rotor air gap magnetic field When the motor is running at no load, the air gap magnetic field is provided by the permanent magnet alone. The generated magnetic field rotates together with the rotor and the rotational speed is synchronous speed.Sep 2, 2020 · In the PMSG that has not been the CT reduction technique, the rotor permanent magnets (PMs) have an increasing effect on the CT since each PM has the same relative position with reference to the stator slots . The CT in each PM is in the same phase as the others, so, the harmonic component of each is added together then, CT has become higher. 2.2 External rotor permanent magnet motor rotor air gap magnetic field When the motor is running at no load, the air gap magnetic field is provided by the permanent magnet alone. The generated magnetic field rotates together with the rotor and the rotational speed is synchronous speed.It should be understood that the “rotor inside” vs. “rotor outside” distinction is in fact trivial, with very few exceptions, which we will note. 2.1 Surface Magnet Machines Figure 1 shows the basic magnetic morphology of the motor with magnets mounted on the surface of the rotor and an otherwise conventional stator winding. Aug 1, 2022 · The axial lengths of the IPM rotor and the SynRM rotor are respectively changed by changing the parameters L and H. It shows that when the width of the permanent magnet L is 85 mm and the thickness H is 4 mm, the maximum total torque reaches 174.2 N m. The length of the permanent magnet rotor is 141.17 mm. Download : Download high-res image (177KB)
Permanent magnet generator (PMG) for vehicles has attracted more and more attention because of its high efficiency, high power density, and high reliability. However, the weak main air-gap magnetic field can affect the output performance and the normal use of electrical equipment. Aiming at the problem, this paper took the rotor …
Eddy current losses in magnets are a major consideration in the rotor design of permanent magnet synchronous motors (PMSMs). Stator design choices and the use of modern inverters with high switching frequency introduce harmonics that can contribute to significant losses in the magnets, causing the rotor to heat up. In typical …A new technique for high performance and robust speed control of permanent magnet synchronous motor (PMSM) using a mixed non-linear H∞ and Sliding Mode Control (SMC) is applied.
where Φ is the magnet flux crossing the air gap, R is the total reluctance through the flux paths and θ is the rotor angle. It is clear that if the reluctance R does not vary as the rotor rotates, then the cogging torque T cog is zero. From this point of view, the cogging torque can be improved by changing the V-shape rotor structure variables …Apr 17, 2022 · Crider, J.M., Sudhoff, S.D.: An inner rotor flux-modulated permanent magnet synchronous machine for low-speed high-torque applications. IEEE Trans. Energy Convers. 30(3), 1247–1254 (2015) CrossRef Google Scholar Reism, K., Binder, A.: Development of a permanent magnet outer rotor direct drive for use in wheel-hub drives. A method of balancing an embedded permanent magnet motor rotor includes the steps of: a) providing a non-magnetic cylindrical shaft having an axis of rotation and a generally cylindrical surface with an even number of recessed slots defining an even number of ribs therebetween; b) machining an axial slot having a cross-section with a top opening, a bottom and two sides in a center portion of ... The permanent magnet synchronous motor (PMSM) is widely used in the electric vehicle and domestic appliance industries. The structure of the PMSM motor varies depending on the permanent magnet arrangement in the rotor structure; among them, the interior permanent magnet (IPM) PMSM motors made by inserting permanent …
In order to get rid of the bulky and lossy differential gears and to enhance the system robustness, the magnetic differential (MagD) system is proposed after the mechanical differential (MechD) and electronic differential (ElecD) systems. The MagD system is mainly composed of the double-rotor (DR) stator-permanent-magnet (PM) …
Arnold produces high performance permanent magnet motor components and sub-assemblies for aerospace and defense, industrial, automotive, and motorsport applications, such as: KERS — Kinetic Energy Recovery System, which includes a composite sleeved RECOMA® SmCo magnet rotor for a 50,000+ RPM, 100KW+ system
In this work, different analytical methods for calculating the mechanical stresses in the rotors of permanent magnet machines are presented. The focus is on interior permanent magnet machines. First, an overview of eight different methods from the literature is given. Specific differences are pointed out, and a brief summary of the …An ironless rotor structure wastes permanent magnet material, since the magnetic circuit closes through air in the rotor side. Therefore, a thin steel rim, to which the magnets are attached, is employed (Fig. 9.1) The rim can be either a laminated structure, in which case the eddy current losses of the rotor remainThe research is devoted to the investigation of NdFeB permanent magnet (PM) based synchronous generators with non-overlapping concentrated windings. The rotor of such …This paper presents a design method of the basic model of high-speed surface-mounted permanent magnet synchronous motor (SPMSM) comprehensively considering the mechanical and electromagnetic properties based on the subdomain method. In the rotor design stage, the mechanical stresses of the permanent magnet …Mar 16, 2015 · A post-assembly magnetizing fixture has been designed and successfully used to magnetize the rotor of a 100 kW high speed permanent magnet synchronous motor. The rotor is a solid cylinder with outer diameter of 80 mm and total length of 515 mm. The permanent magnet material is samarium-cobalt (Sm 2 Co 17) with saturation magnetizing field of 6 ...
As shown, it mainly consists of permanent magnet rotor (PMR) and conductor rotor (CR). The CR is composed of two rotors, each of which contains copper sheet (CS) and corresponding back iron. The PMR is divided into flux-adjustable rotor (FAR) and fixed flux rotor (FFR), each of which adopts spoke-mounted PMs magnetized …Apr 17, 2022 · Crider, J.M., Sudhoff, S.D.: An inner rotor flux-modulated permanent magnet synchronous machine for low-speed high-torque applications. IEEE Trans. Energy Convers. 30(3), 1247–1254 (2015) CrossRef Google Scholar Reism, K., Binder, A.: Development of a permanent magnet outer rotor direct drive for use in wheel-hub drives. This paper proposes a novel layered permanent magnet motor (N-LPM), which is based on a three-degree-of-freedom (3-DOF) permanent magnet motor. Compared with the former, the improved N-LPM air gap magnetic density, torque and structure stability have been significantly improved. The proposed N-LPM has three …Aiming at the rotor strength problem of high speed permanent magnet synchronous motor (HSPMSM), a design method for maximum outer diameter of permanent magnet is proposed. Firstly, on the basis of mechanics of materials, the stress analytical model of HSPMSM rotor with anisotropic material is established. Then, the …More specifically, the rotor itself contains permanent magnets, which are either surface-mounted to the rotor lamination stack or embedded within the rotor …Feb 21, 2023 · An interior permanent magnet synchronous motor (IPMSM) with ‘VV—’ shape rotor topology structure is proposed. The established two-dimensional (2D) parameterized finite element analysis (FEA) models are used to analyze and compare the output average torque, torque density, air-gap flux density and back electromotive force (EMF) of the IPMSM with ‘V’ shape, ‘V—’ shape, ‘VV ...
effects of magnet polarities [18,19], PM number [20], winding configurations[21,22], asymmetrical stator pole [23], stator/rotor combinations [24] etc., and their effects on electromagnetic characteristics have been presented. Further more, investigations of the working mechanism have demonstrated that only fundamental rotor permeance andIn order to get rid of the bulky and lossy differential gears and to enhance the system robustness, the magnetic differential (MagD) system is proposed after the mechanical differential (MechD) and electronic differential (ElecD) systems. The MagD system is mainly composed of the double-rotor (DR) stator-permanent-magnet (PM) …
In many high-speed electrical machines, centrifugal forces within the rotor can be first-order constraints on electromagnetic optimization. This can be particularly acute in interior permanent magnet (IPM) machines in which magnets are usually retained entirely by the rotor core with no additional mechanical containment. This study …Magnet Rotors. Magnetic rotor, or permanent magnet rotor is the non stationary part of a motor. The rotor is the moving part in an electric motor, generator and more. Magnetic rotors are designed with multiple poles. …This paper is focused on the optimal design, simulation, and experimental testing of a counter-rotating double-rotor axial flux permanent magnet synchronous …Electromagnetic interaction between the rotor permanent magnet and the stator slots is quite large. (1000 N simulated value for this motor). The air-gap needs to be as small as 1 mm. Fig. 4a shows the single disc of rotor with 9° skewed permanent magnets. The machine rotors were constructed by using mild-steel.Jul 1, 2017 · Unbalanced magnetic force (UMF) is one of the most important issues in permanent magnet (PM) machines with rotating asymmetric winding configurations, where the UMF is intrinsic [1, 2]. When these machines are perfectly manufactured, they show good electromagnetic performances such as high efficiency, high torque density, low torque ripple and ... Apr 1, 2023 · The rotor spinning at high speed generates a large tensile stress. Once the yield strength of the permanent magnet (PM) is exceeded, the permanent magnet will be broken. Therefore, a high-strength sleeve must be installed outside the permanent magnet [3, 4]. Many researchers have conducted extensive study on rotor strength analysis of HSPMSM ... The development of high-speed (operating at a rotation speed above 10,000 rpm) synchronous electric machines with permanent magnets is currently a relevant design direction [1,2,3,4,5].The structure of the rotor of synchronous machines with permanent magnets is a system of permanent magnets kept from their radial movement with the …Structure Review of Inner Permanent Magnet Synchronous machines (PMSM) Radial magnetization pattern can used applied to the permanent magnet motors, motors are in different size and shapes for the different applications. In this section different kind of PM motors will be reviewed. Field Excitation (FE) Permanent Magnet (PM) …Today’s automotive industry has focused its studies on electric vehicles (EVs) or hybrid electric vehicles (HEVs) rather than gasoline-powered vehicles. For this reason, more investment has been made in electric motors with high efficiency, high torque density, and high-power factor to be used in both EVs and HEVs. In this study, an outer-rotor …
Jun 23, 2022 · The rotor overtemperature caused by losses is one of the important issues for the high-speed electrical machine. This paper focuses on the rotor loss analysis and CFD-thermal coupling evaluation for 105 kW, 36,000 r/min HSPMSM. Three types of sleeve materials as carbon-fiber, Titanium alloy, and stainless steel are introduced in this paper, researching the effects of sleeve conductivity ...
The rotor overtemperature caused by losses is one of the important issues for the high-speed electrical machine. This paper focuses on the rotor loss analysis and CFD-thermal coupling evaluation for 105 kW, 36,000 r/min HSPMSM. Three types of sleeve materials as carbon-fiber, Titanium alloy, and stainless steel are introduced in this paper, …
When permanent magnet synchronous motor is running at ultra-high speed, the tensile strength of permanent magnet is far lower than the compressive strength, and it is unbearable to withstand the large centrifugal tension caused by rotation. Generally, adding the non-magnetic alloy sleeve outside the permanent magnet is the protective …Abstract: For the high-frequency permanent magnet electrical machine, a reasonable mechanical aspect design is crucial to meet its stability and reliability. This study focuses on the accurate modelling and analysis of the natural frequencies and modes of the rotor assembly for a designed and manufactured 100 kW 32,000 r/min motor.A magneto-structural combined dimensional and topology optimization approach for interior permanent magnet synchronous machine (IPMSM) rotor design is proposed using the solid isotropic material with penalization (SIMP) density-based topology optimization method. This method optimizes the location and dimensions of the …The nite element results show that the modular rotor permanent magnet ux switching machine has greater torque than salient rotor FEFSM, HEFSM, and PMFSM at the rated load with signicantly less weight than the others. Keywords Back EMF · Electromagnetic torque · Field Excitation · Hybrid Excitation · Modular rotor PMFSM · Permanent magnet Permanent Magnet Rotors High-Speed, High-Reliability, High-Efficiency Permanent Magnet Rotors For over 25 years, Integrated Magnetics has developed and refined the expertise needed for the technical design and manufacturing of high-speed, high-reliability, high-efficiency permanent magnet rotors for high-performance electrical machines. Based on the complex structural characteristics of permanent magnet-assisted synchronous reluctance motors (PMA-SynRMs), this paper proposes a multi-objective optimization design method for the motor using a composite algorithm. Firstly, the power density, electromagnetic torque, cogging torque, and torque fluctuation coefficient …Lee et al. (5, 6) proposed a rotor supported by the permanent/electromagnetic magnetic bearing (PEMB) to operate well under the control of four simple analog PD controllers. In this study, the design considerations of the PEMBs and the method for analyzing the complete rotor-bearing system are presented. Also, a …An interior permanent magnet synchronous motor (IPMSM) with ‘VV—’ shape rotor topology structure is proposed. The established two-dimensional (2D) parameterized finite element analysis (FEA) models are used to analyze and compare the output average torque, torque density, air-gap flux density and back electromotive force …The nite element results show that the modular rotor permanent magnet ux switching machine has greater torque than salient rotor FEFSM, HEFSM, and PMFSM at the rated load with signicantly less weight than the others. Keywords Back EMF · Electromagnetic torque · Field Excitation · Hybrid Excitation · Modular rotor PMFSM · Permanent magnet Aiming at the rotor strength problem of high speed permanent magnet synchronous motor (HSPMSM), a design method for maximum outer diameter of permanent magnet is proposed. Firstly, on the basis of mechanics of materials, the stress analytical model of HSPMSM rotor with anisotropic material is established. Then, the …
Recently, PMSMs having high power density and high efficiency are widely used in premium home appliances and electric vehicles. 1 Compared to a SPMSM (surface-mounted permanent magnet synchronous motor), large torque ripple in an IPMSM is a bad influence on the system in a variable speed range. 2 The optimization of a motor is …Mar 20, 2021 · Reluctance is a function of rotor position in a variable reluctance motor. Sequential switching (Figure below) of the stator phases moves the rotor from one position to the next. The mangetic flux seeks the path of least reluctance, the magnetic analog of electric resistance. This is an over simplified rotor and waveforms to illustrate operation. A computationally efficient design of interior permanent magnet (IPM) motor rotor features is investigated utilizing analytical methods. Over the broad operating range of IPM machines, interactions of MMF sources, permeances, and currents result in torque harmonics. The placement of traditional rotor features along with sculpt features are …In their work, a range of electric machine options are considered and it is concluded that a synchronous machine with a permanent magnet (PM) rotor will be the most efficient and power dense. In addition to applications in turbocharging, Gerada [ 3 ] highlight an increasing demand for high-speed electrical machines in flywheel energy …Instagram:https://instagram. jerseysbubbapercent27s 33 clarksville menuku womenpercent27s basketball tv scheduleclosest atandt to my location Dual Rotor Axial Flux Generator (DRAFG) is a permanent magnet axial flux generator commonly used for low speed power generation using wind power. This generator can generate useful amount of ... downloads erwachsene.htmpick 3and4 md lottery drawing Metrics. Permanent magnets constructed from metal ions and organic linkers using molecular design principles could bring transformative advances in areas such as energy conversion, transportation ...Purpose This paper comprehensively analyses the radial electromagnetic (EM) force by unit area and vibration characteristics in a permanent magnet synchronous motor (PMSM). This provides the possibility to verify the action law, causes, and influencing factors of vibration deformation and provides new ideas for vibration management. … atandt gigabit internet availability 1. Introduction. At present, the low-speed high-torque transmission system has vast application prospects in the application fields of ship propulsion, lifting, mining and oil field exploitation [1].Permanent magnet motors can maintain good performance in a wide range of load changes, so they have received extensive attention in low-speed and large …In the same way in , through FEM simulations and experimental results, a simple dynamic abc model for brushless permanent magnet motors, under demagnetisation faults, is presented and validated. The strategies based on the analysis of the harmonics produced by rotor demagnetisation in the phase currents or the EMF are …